Quality control is a key factor in the production of laminated insulation material. It ensures that the product meets all safety, efficiency, and performance criteria before it enters the market. Quality control plays an important role in minimizing errors, defects, and delays while producing this critical material.
With quality control processes in place, manufacturers can be confident that their products will meet or exceed customer expectations and provide consistent results over time. This article delves into why quality control is so important for producing reliable laminated insulation materials, how it works to reduce risks associated with manufacturing them, and how companies can ensure they are adhering to proper quality standards as part of their production process.
Benefits of Quality Control in Laminated Insulation Material Production
Quality control is essential in the production of laminated insulation materials. Not only does it ensure that the material meets industry standards and customer expectations, but there are also many benefits to having a quality control system in place. By implementing an effective quality control process, manufacturers can improve product safety and reduce the risk of costly issues later on. Quality control tests can help identify potential problems before they become serious defects and lead to costly repairs or recalls down the line. Additionally, by regularly checking for any irregularities or faults throughout production, manufacturers can guarantee that their products meet all applicable health and safety regulations as well as any other specified requirements. Another advantage of having a quality control system is improved customer satisfaction levels due to higher-quality products being produced consistently from batch to batch. Customers will be more likely to purchase materials from a manufacturer who has taken steps to ensure their products are reliable and up to standard – this could translate into increased sales over time too! Finally, regular quality checks during manufacturing processes can help Laminated Insulation Material producers save money by avoiding situations where defective materials need replacing or reworking at great expense. Not only will this mean fewer wasted resources but it also means less time spent manually inspecting each piece which could free up staff for other activities instead!
Critical Steps for Ensuring Quality in Laminated Insulation Manufacturing
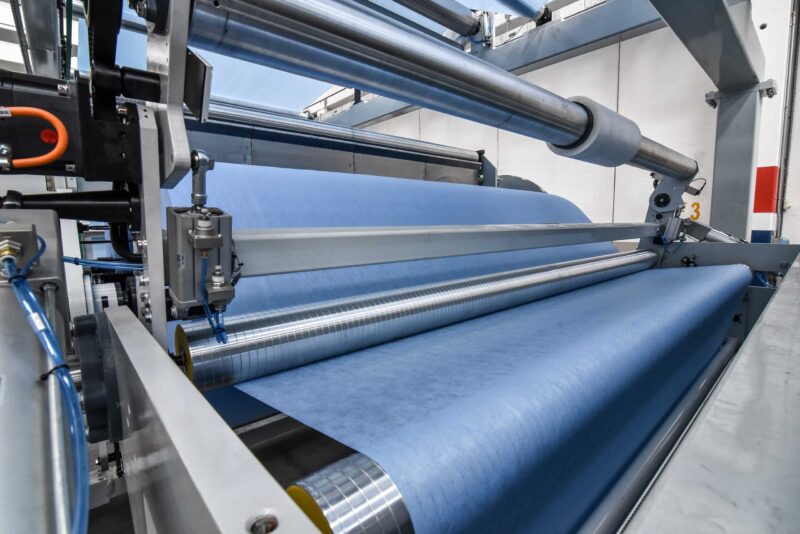
Quality control is an essential part of the production process for laminated insulation materials. It involves a series of steps to ensure that all parts of the manufacturing process are operating efficiently and delivering high-quality products.
Critical steps for ensuring quality in laminated insulation production include implementing proper product testing, inspecting raw materials, monitoring equipment performance, enforcing safety measures, and instituting post-production testing protocols. Product testing is critical to guarantee the quality of the finished material. Tests should be conducted regularly during production to identify any potential issues with components or processes before they become serious problems leading to costly rework or rejections.
Inspecting raw materials used in lamination can also help detect possible defects early on so that corrective actions may be taken before further damage occurs down the line. The performance of machinery and tools used in lamination should also be monitored closely throughout the entire process since faulty or outdated machines can cause significant delays in production as well as reduced output quality levels which could affect customer satisfaction negatively.
Implementing safety measures such as protective gear, guards and signage will help minimize accidents while working with these types of materials while also reducing potential liabilities associated with poor work practices or negligence. Post-production tests must also take place after each batch has been completed to ensure compliance with industry standards and customer specifications prior to shipping out orders from your facility.
The Impact of Poor Quality on the Performance of Laminated Insulation Materials
The quality of laminated insulation materials is paramount for their performance. Poorly produced materials can cause a variety of issues, ranging from premature failure to reduced efficiency. As such, it is essential that the production process follows strict quality control protocols in order to ensure that the end product meets certain requirements.
One negative consequence of poor-quality laminated insulation materials is increased energy usage due to decreased thermal resistance and air infiltration rates. Low-grade material may not be able to maintain consistent temperatures across its surface or resist external factors like wind and moisture which can lead to structural damage as well as significant energy waste.
In addition, poor-quality lamination techniques may result in weakened bonds between components leading to delamination over time and further compromising the integrity of these products. Moreover, another major issue associated with low-quality production standards relates to safety concerns since faulty installations done with substandard material can have a number of hazardous outcomes such as electrical shock or fire hazard when exposed directly with high-voltage power lines or flames respectively.
Furthermore, malfunctioning equipment caused by lower-grade insulation layers could potentially harm users during operation thus making proper manufacturing processes even more important for protecting consumer welfare and avoiding costly liabilities later on down the line. In conclusion, it is clear that maintaining stringent levels of production standards when creating laminated insulation materials is highly necessary in order for them to perform optimally without compromising user safety along the way.