As car production moves towards a more sustainable future, the need for efficient and effective press brakes is becoming increasingly important. Manufacturers must find ways to reduce waste and improve efficiency while maintaining high safety standards.
Environmental considerations are paramount when it comes to producing cars that have minimal impact on our planet’s resources. This article will explore how modern press brake technology can help manufacturers achieve their goals of sustainability in car production without sacrificing quality or safety.
It will discuss the benefits of using new technologies such as servo-electric presses, intelligent software programs, and advanced materials that enable greater accuracy with less waste material produced. We also consider how dedicated press brake operators can make a difference by utilizing best practices to minimize environmental impacts during the manufacturing process.
Finally, will analyze what needs to be done for these advancements to become standard practice within the industry as well as look at potential areas where further research could be beneficial for sustainable car production.
Energy Consumption and Efficiency of Press Brakes
Press brakes are an essential tool in automotive production, helping to shape metal into the required parts for car manufacturing. When it comes to environmental considerations, understanding the energy consumption and efficiency of press brakes is key.
Efficiency can be increased by optimizing press brake speed settings according to the material being processed as well as by using optimized back gauge systems that help reduce cycle times. Additionally, hydraulic presses consume less power than mechanical ones, making them a more efficient choice when it comes to reducing energy consumption.
Automation helps improve energy efficiency even further: robot-assisted feeding decreases the idle time between cycles and eliminates non-productive manual activities like measuring pieces and sorting scrap; automatic die-changing systems allow for faster setup changes with reduced operator intervention; computer numerical control (CNC) machines minimize human error leading to higher quality parts with fewer rejects while eliminating the need for manual programming adjustments or corrections along the way.
In short, thanks to recent advancements in technology manufacturers have access to improved solutions which can substantially increase both the energy efficiency and productivity of their press brake operations – an important factor when considering sustainable car production methods today.
Pollution Reduction Through the Use of Press Brakes
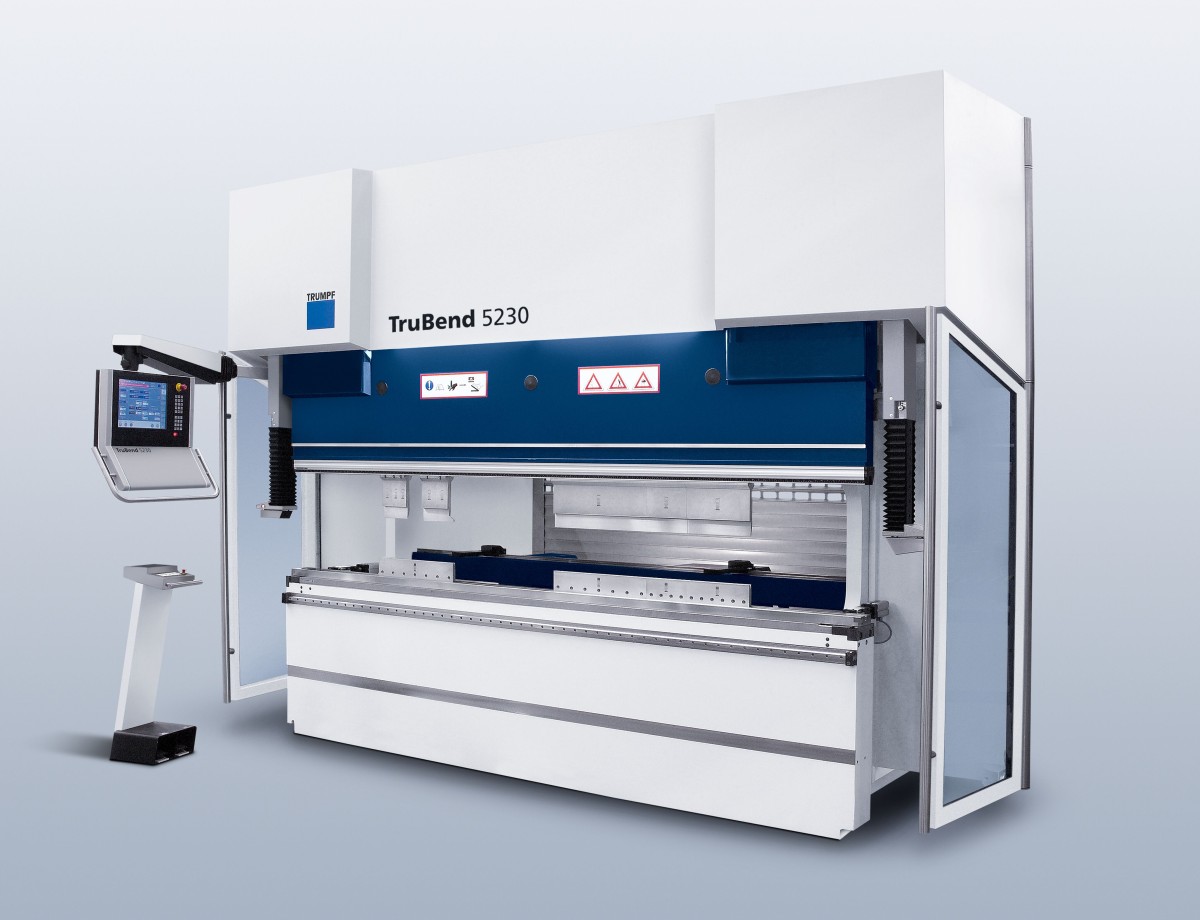
In the age of sustainable car production, press brakes are a valuable tool for reducing pollution and waste. By using press brakes to create parts with exact precision, manufacturers can reduce material wastage that would otherwise be discarded due to being too large or imperfectly shaped.
In addition, these machines also produce parts with fewer imperfections than manual methods, reducing the need for costly rework later in the process. Furthermore, by utilizing a wide range of settings and parameters available on modern press brake models, manufacturers can minimize energy consumption while increasing productivity.
This helps reduce their carbon footprint and contributes to overall environmental sustainability goals in the industry. All in all, press brakes offer a reliable solution that is both cost-effective and environmentally friendly when used correctly.
Reducing Waste Products From Press Brake Operations
Press brake operations are essential to the car production process, but they can also be a source of environmental waste. Reducing and minimizing waste products from press brakes is an important step in achieving sustainable car production.
By optimizing processes, manufacturers can minimize materials used and ensure that no resources go to waste. Manufacturers should strive to use more efficient methods, such as using only the amount of force needed for each job or switching from manual systems to automated ones with repeatable accuracy levels.
This will help eliminate excess material usage while maintaining quality standards. Additionally, manufacturers should focus on implementing safety protocols such as proper ventilation and dust collection systems to reduce airborne emissions from press brake operations.
Other solutions include utilizing advanced tools like laser cutting machines which provide higher precision than traditional metal cutting methods while reducing scrap generation rates considerably due to their ability to produce parts with minimal edge burrs and precise cuts every time. Furthermore, investing in regular maintenance services for press brakes helps keep them running at optimal efficiency while reducing energy consumption over time – a win-win situation for both the environment and your bottom line!
Sustainable Materials for Press Brake Manufacturing
The increased demand for sustainable car production has been a high priority across the automotive industry, and press brakes are an integral part of the manufacturing process. As such, it is essential to ensure that these machines use materials that are in line with sustainability goals.
Using recycled materials can help reduce environmental impact during press brake operations, as well as minimize costs. However, there are some considerations when selecting these materials; they must be able to withstand extreme temperatures and pressures without compromising on performance or safety.
Additionally, sourcing them should not add any additional emissions or pollutants into the atmosphere. Aluminum alloys have become increasingly popular for their lightweight yet durable properties which make them ideal for press brake operations.
Copper-based alloys also provide excellent thermal conductivity and electrical insulation while having low toxicity levels compared to other metals commonly used in production processes like steel or titanium alloys. Carbon fiber composites are another option due to their strength-to-weight ratio but require more careful handling than traditional metals since they cannot absorb impacts well and may need special protective coating before being used in manufacturing applications like press brakes.
Overall, when choosing sustainable materials for press brake manufacturing, it is important to consider both cost savings potential and environmental impact so that manufacturers can identify options that meet both criteria without sacrificing the quality or safety standards of production equipment
Recycling Options for Used or Damaged Parts From Press Breaks
With the growing demand for sustainable car production, press brakes present a unique challenge for environmental consideration. Recycling used or damaged parts from press brakes can help to reduce the amount of waste created in manufacturing and save valuable resources.
There are several options available for those looking to recycle these materials responsibly. The first option is to reuse the components from older machines by refurbishing them with new parts and making them ready to use again.
This helps eliminate unnecessary disposal costs while reducing the need for additional raw materials in production processes. Additionally, some manufacturers offer end-of-life recycling programs that pay cash incentives when customers return their old products instead of disposing of them in landfills.
Another viable option is to donate used or damaged press brake parts to organizations that use them as part of educational programs or research projects. This not only allows students access to hands-on learning opportunities but also prevents potentially hazardous components from entering landfills where they may pose an environmental hazard due to improper disposal methods such as burning or dumping into water sources like rivers and lakes.
Finally, some companies specialize in recycling metals such as aluminum and steel which can be invaluable resources when it comes time to dispose of large amounts of material generated during manufacturing activities. These services provide a safe way for businesses and individuals alike to recycle their scrap metal while helping protect the environment at the same time
Conclusion
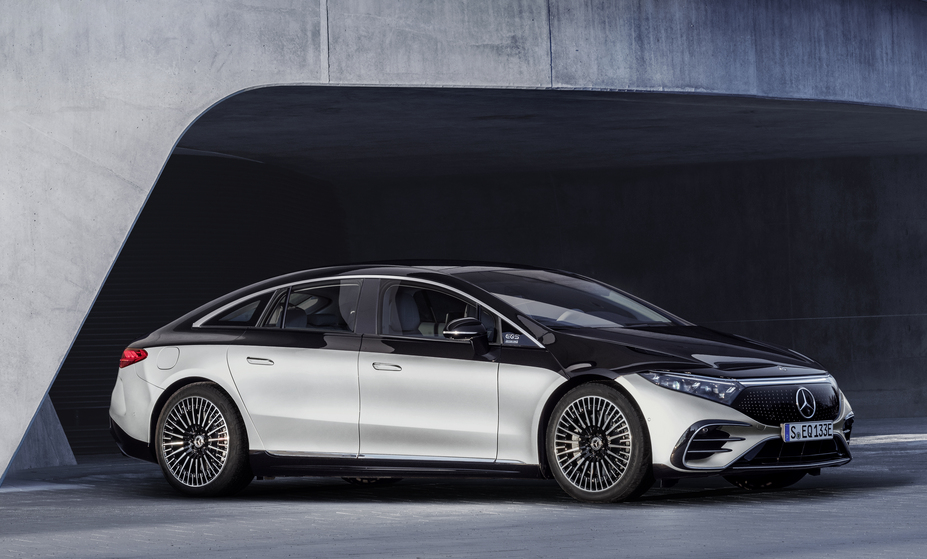
In conclusion, press brakes are an integral part of producing sustainable cars. As vehicles become more lightweight and efficient, so too must the tools used to produce them.
By leveraging advanced technology like precision press brake dies, automotive manufacturers can create parts that meet environmental standards while still offering a high level of quality and performance. This is essential for creating the best possible product for consumers who care about their impact on the planet.