Longitudinal Submerged Arc Welding (LSAW) pipes are an essential tool for many industries, from the oil and gas sector to engineering and construction. They offer a range of benefits including strength, longevity, and versatility compared to traditional welding techniques.
This article will delve into the various components of LSAW pipes as well as their advantages over competing technologies. Well-examine common applications for these pipes and explore some tips on how to get the most out of them in your projects.
Finally, will discuss why they’re so popular with professionals across multiple fields. Get ready to learn more about this cutting-edge technology!
Advantages of Longitudinal Submerged Arc Welding
Longitudinal Submerged Arc Welding (LSAW) is an efficient and cost-effective way to join two pieces of steel. It is a welding process that enables welders to produce high-quality, consistent welds with minimal distortion.
LSAW has many advantages over traditional welding techniques, making it an ideal choice for the construction of pipelines and other large structures. The first advantage of LSAW is its speed – it can be applied quickly and efficiently without compromising on quality or accuracy.
This makes it one of the most popular choices for manufacturers who need to produce large volumes in a short period. Furthermore, LSAW produces less heat than other welding methods which helps to reduce shrinkage and warping at the joint edges during cooling after completion.
This leads to more accurate production when compared with alternative processes such as oxyacetylene welding (OAW). Another big advantage provided by Longitudinal Submerged Arc Welding comes from its ability to work with thicker materials than traditional arc welding techniques can handle; making it possible for fabricators to use heavier gauge material in their projects while still maintaining quality results.
This opens up new possibilities within manufacturing due to increased strength being available from this type of joining method – particularly useful when constructing larger scale items such as pipes or structural frames where greater strength may be required for safety reasons over thinner alternatives used in OAW or manual arc welding (MAW). Finally, like all arc welding processes, there are no consumables involved in Longitudinal Submerged Arc Welding meaning that costs remain low throughout the entire life cycle of any given project; another major benefit when looking at long-term investments into infrastructure development such as pipeline building initiatives across various industries including oil & gas exploration sites worldwide
Exploring Different Types of LSAW Pipe Construction Techniques
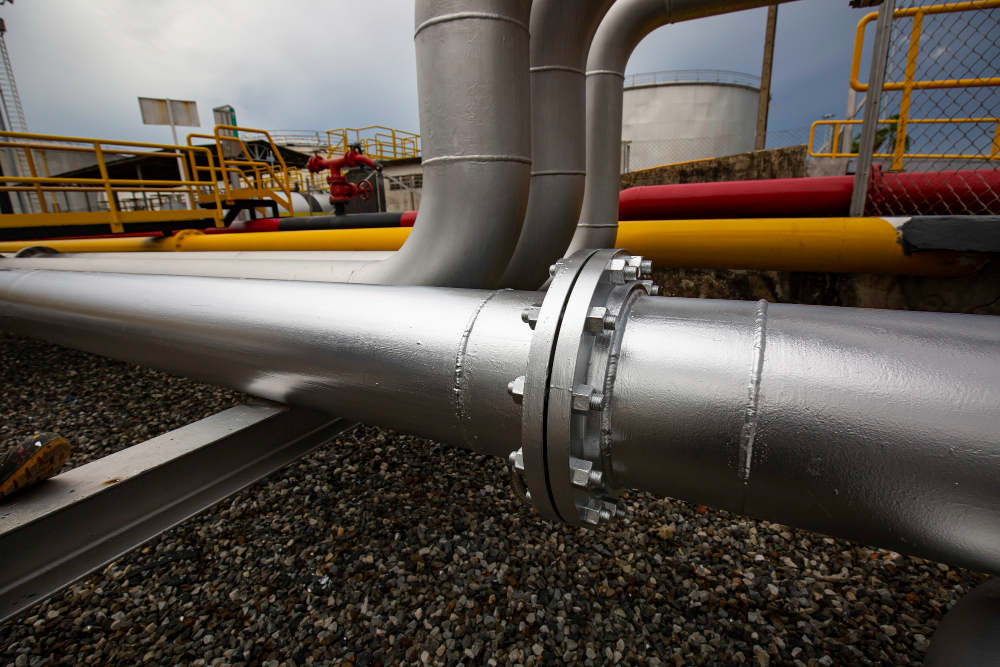
Longitudinal Submerged Arc Welding (LSAW) pipes are a type of pipe construction technique that has been used in different industries for decades. This welding method is preferred as it produces stronger and more durable welds compared to other techniques.
The process consists of longitudinally joining two pieces of metal using heat generated from an arc between the electrodes and the workpieces. The first step in LSAW pipe construction involves preparing the edges of each metal piece by smoothing them with grinding tools, which helps ensure a strong weld joint later on. Once these edges have been properly prepared, they are then positioned together so that an arc can be created between them to generate enough heat for fusion welding.
It’s important to note that this procedure requires greater skill than other forms of welding due to its complexity and precision requirements; however, when done correctly, it results in highly reliable welds that will last for many years. Another type of LSAW pipe construction technique is known as U-O or U-Vee Ogee Welding which utilizes multiple arcs rather than one single arc like regular LSAW does.
This approach uses multiple arcs simultaneously along two separate paths ensuring even distribution across both sides while also providing stress relief at critical points along the length of the joint. As a result, this type of welding yields superior quality joints compared to those produced via traditional methods such as SMAW or GMAW techniques.
Finally, there is spiral submerged arc welding (SSAW), where instead of generating a straight line weld down each side like with standard LSWAW processes, SSAWs utilize continuous helices around the circumference resulting in higher strength joints with less material loss during the manufacturing process making them especially suited for large diameter applications that require additional reinforcement and support over longer distances without sacrificing integrity or durability of the finished product. Overall various types of Longitudinal Submerged Arc Welding Pipes offer distinct advantages depending on application whether it’s requiring high-strength joints over long distances or superior quality connections between varying materials; all allowing engineers greater versatility when designing piping systems tailored specifically towards their needs while still meeting safety standards
Quality Assurance for LSAW Pipes Through Manufacturing Processes

Quality assurance for Longitudinal Submerged Arc Welding (LSAW) pipes is of utmost importance in the manufacturing process. To ensure that only high-grade products are produced, pipe manufacturers must check each component of the welding process to guarantee it meets industry standards.
This requires a thorough examination and testing of all aspects, such as weld quality, joint integrity, material selection, and post-welding heat treatments. By applying these checks throughout production stages, it is possible to eliminate any potential defects before they become an issue further down the line.
As well as using advanced technology such as X-ray imaging or ultrasonic testing to detect problems early on in the production cycle, manual inspections can also be carried out by trained professionals who have been certified to do so. With this combination of modern techniques and experienced personnel working together with one common goal – producing top-quality LSAW pipes – producers can guarantee their customers receive nothing but the best when it comes to welding components and materials.
Identifying Applications and Industries for Longitudinal Submerged Arc Welded Pipes
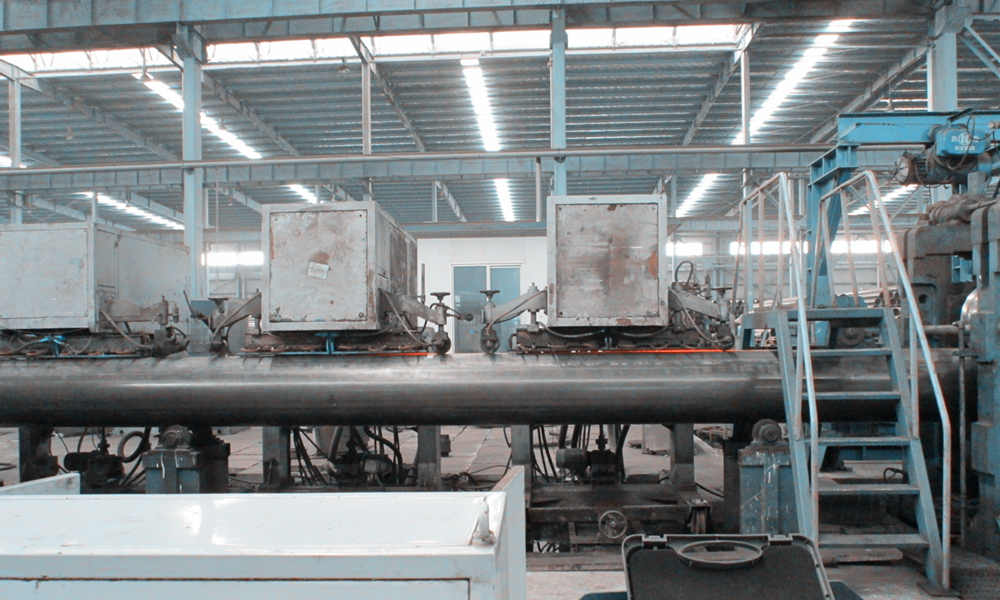
Longitudinal Submerged Arc Welded (LSAW) pipes are increasingly being adopted due to their strong structural integrity, relatively low cost, and versatility. While they may not be as widely used as other welding techniques, LSAW pipes offer several advantages that make them attractive for certain applications and industries.
Identifying Applications and Industries for Longitudinal Submerged Arc Welded Pipes: There are numerous industries where LSAW pipes can prove invaluable in the construction process. From industrial piping to subterranean engineering projects, this type of pipe is suited to almost any job involving fluid transfer or structural support.
It is most commonly seen in oil & gas pipelines spanning long distances as well as wastewater treatment plants with complex networks of channels beneath the surface. Additionally, it has been used extensively in marine operations such as bridge piers and offshore platforms which require robust underwater structures that must stand up against the elements over time.
In addition to its wide range of applications across industries, one of LSAWs’ main benefits lies in its ability to provide superior strength while still utilizing less raw material than other welding methods such as Electric Resistance Welding (ERW). This makes it an excellent choice for projects where weight savings are important – like large vessels carrying heavy loads or overhead highway bridges with limited load-bearing capacity – but also means it can be more eco-friendly when compared with traditional welding techniques.
Ultimately this helps reduce costs without compromising on quality or safety standards expected by industry regulators around the world.
Conclusion
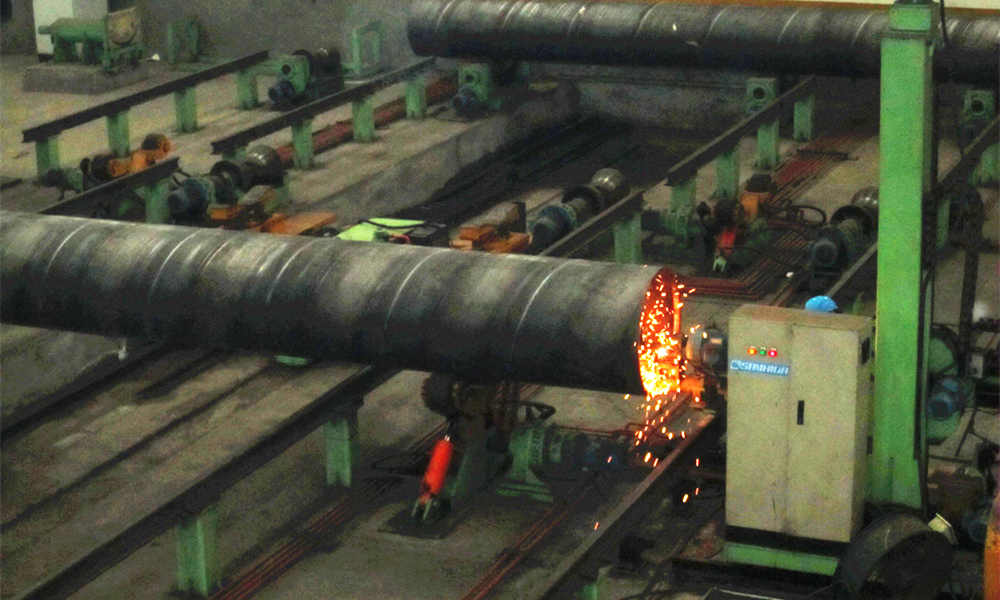
The LSAW pipe is one of the most reliable and efficient methods of Longitudinal Submerged Arc Welding. It offers superior weld integrity, increased strength, improved corrosion resistance, and a lower overall cost than other welding techniques.
With its ability to produce high-quality welds in a wide range of materials, it is suitable for any application needing strong joints and durable structures. It can also be used in many different industries including automotive manufacturing, petrochemical processing, shipbuilding, and construction.
The LSAW pipe has proven itself as an indispensable part of modern industry due to its versatility and reliability.